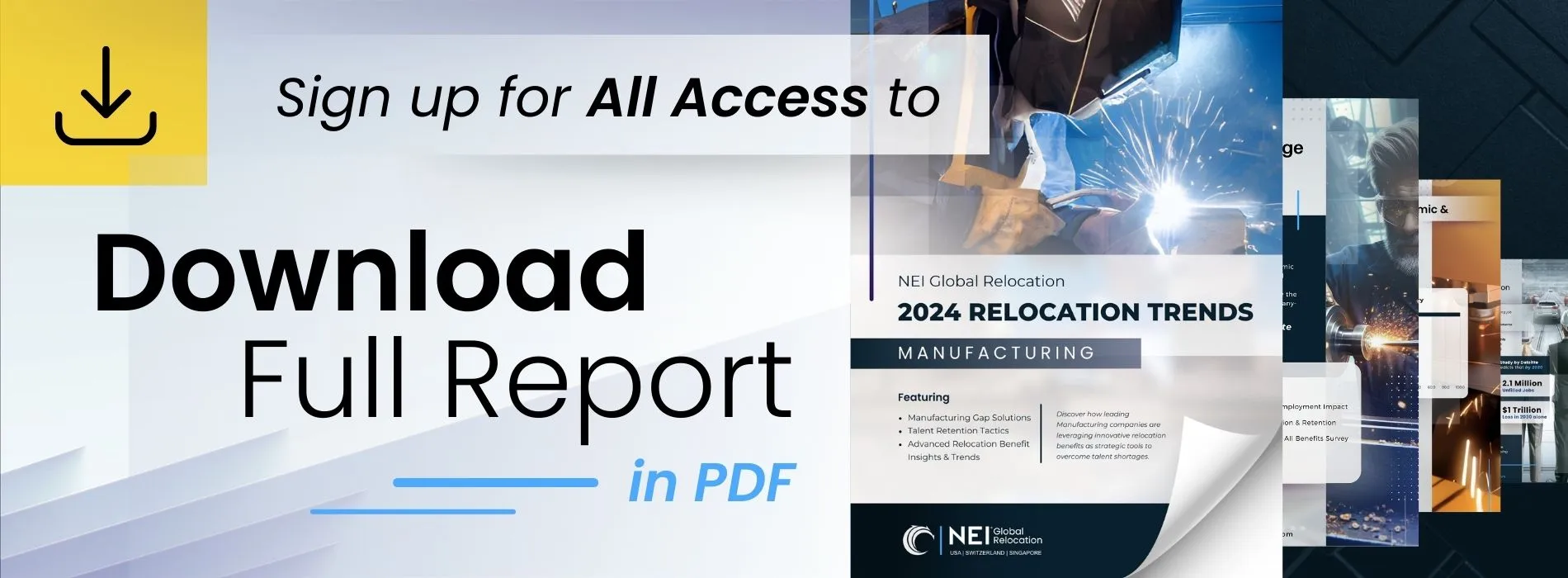
The Talent Shortage is Not Temporary
“Manufacturers are expected to face economic uncertainty, the ongoing shortage of skilled labor, lingering and targeted supply chain disruptions, and new challenges spurred by the need for product innovation to meet company-set net-zero emissions goals.” ~ Deloitte
Manufacturing accounts for about 11 percent of U.S. GDP and employs approximately 8 percent of the U.S. workforce, but U.S. manufacturing jobs have declined from 19.6 million in 1979 to nearly 13 million by November 2022 – a significant 56 percent decrease when adjusted for population growth.
Yet, as of August 2023, 616,000 U.S. manufacturing job openings are still needing to be filled. The industry’s talent shortage, per Betterworks Engage, can be attributed to:
- Outdated perceptions that manufacturing jobs aren’t safe, clean, or progressive
- Misconceptions by younger generations that manufacturing lacks competitive wages
- Perceived lack of investment in employee growth and development
- Not enough STEM graduates with specific skill sets and abilities to meet demand
- A quarter of the industry’s skilled worker base retiring, with more to come in the next decade
In fact, 77% of manufacturers say this shortage is not temporary and there will be ongoing difficulties attracting and retaining workers in the industry.
The manufacturing skills gap in the U.S. could result in 2.1 million unfilled jobs by 2030, according to a study by Deloitte and The Manufacturing Institute. The cost of those missing jobs could potentially total $1 trillion in 2030 alone. This is true for both talent skilled in the design and operation of old and new machinery, as well as the usual positions that are always needed across manufacturing companies to conduct business.
To attract new talent from various sectors, manufacturers must bridge the gap between the expectations of job seekers and the reality of manufacturing jobs, as highlighted by a Deloitte Global Human Capital Trends study. It's crucial for these companies to focus on widening their talent pool, fostering inclusive work environments, and committing to ongoing skill development to ensure future success.
Key Findings from NEI’s Global Relocation’s 2023 All Benefits Survey
To address these shortages, manufacturing industry Talent Management and HR teams will have to evolve and maximize relocation efficiency and effectiveness to secure talent and retain employees. This starts with examining the benefits used today and ensuring they are ready for tomorrow.
Notable findings from Manufacturing companies participating in NEI Global Relocation’s 2023 U.S. Domestic All Benefits Survey include the following:
Partial Lump Sum
- Manufacturing companies tend to favor a Partial Lump Sum program to cover certain benefits such as temporary living, home finding, return trips, final move and miscellaneous expense allowance.
- A partial lump sum was offered by 31 – 67% of Manufacturing companies (depending on employee level) as compared to 30 – 51% of participants in all industries combined.
Economic Impact on Policy
- Unlike other industries, Manufacturing has not increased COLA, MIDA or Lease Cancellation due to economic changes, choosing instead to stay the course.
- Many companies in NEI’s U.S. Domestic All Benefits Survey (all industries combined) have reviewed and revised policy components to adjust to the changing market.
Home Sale Trends and Responses
A strong sellers’ market over the past few years has caused many companies in multiple sectors to tighten up their home sale programs, scaling down benefits to save money without significantly impacting employees. As the market pendulum starts to swing back to the buyers’ favor, companies are beginning to consider ways to enrich their home sale programs again.
- BVO is preferred over GBO by Manufacturing participants. BVO is offered by 7 – 47% of Manufacturing participants compared to 5 – 33% of participants in all combined industries.
- GBO is offered by 0 – 35% of Manufacturing participants compared to 1 – 43% of participants in all combined industries.
- Loss on Sale is offered by 0 – 20% of Manufacturing participants compared to 1 – 34% of participants in all combined industries.
Tax Treatment
- Manufacturing participants were less likely to gross-up origination services(e.g. partial lump sum, home sale reimbursements, miscellaneous expense allowance), and yet more likely to gross-up destination services (e.g. temp living, rental finding assistance, home finding trip).
- Of Manufacturing participants, 45% complete year-end true up calculations compared to 34% of participants in all combined industries.
In summary, manufacturing companies lean towards more conservative relocation policies, such as favoring Partial Lump Sum programs and maintaining steady course on COLA, MIDA, or Lease Cancellation policies despite economic shifts. This approach is distinct from broader industry trends, where companies are revising policies to adapt to market changes.
A company within the manufacturing sector that adopts a more robust and forward-thinking relocation policy not only differentiates itself but also has a golden opportunity to secure and retain the industry's best talent. As the landscape evolves, those willing to enhance their benefits in thoughtful ways could obtain a sizable competitive advantage.
Investing in Future Competitiveness Today: The Role of Relocation
“Manufacturing is no longer the old-fashioned assembly-line industry of yesteryear. Manufacturing today is taking center stage as an electrifying industry full of possibilities.” ~ Forbes
With expense reduction top of mind for many, it is imperative for Manufacturing companies to identify and consider cost savings opportunities, but also leverage innovative relocation services, technologies, and expertise when addressing talent needs.
NEI Global Relocation strives to be in complete alignment with each client’s priorities, business objectives, and talent management goals.
When choosing the best global relocation management partner, look for a trusted, stable firm with experienced professionals and extensive global networks. A partner that will deliver you the best return on investment, proactively advise you on current and future trends, and support your efforts to secure and relocate talented candidates.
For more information, please contact your NEI representative.
About NEI Global Relocation
NEI is a certified Women’s Business Enterprise headquartered in the U.S. with in-region offices and teams in Switzerland and Singapore. As a full service, global relocation and assignment management company that partners with clients across the globe to provide consultative guidance and solutions, NEI has over 200 clients including many Fortune 500 and Fortune 1000 corporations and we support client Tier 1 and Tier 2 supplier diversity goals each year. For more information and other articles, see www.neirelo.com.
The above article is provided for informational purposes only. Please consult your tax, legal, or accounting advisors before making any decisions or transactions.
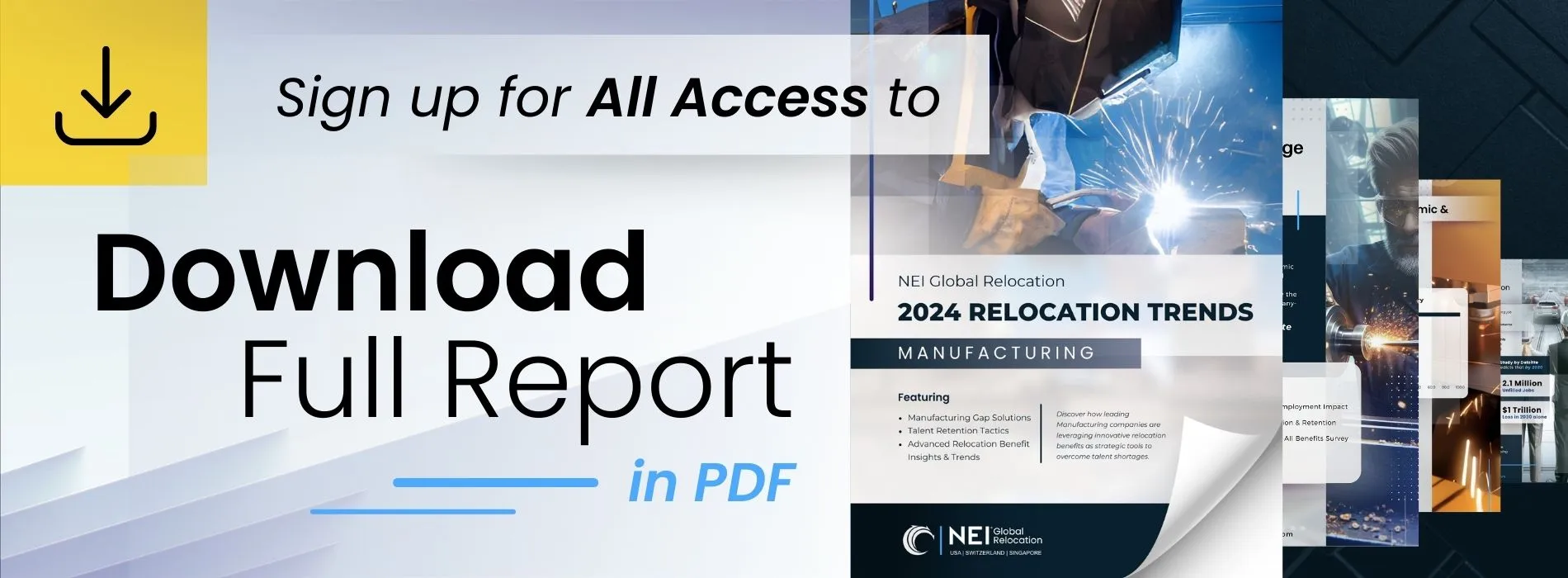
The Talent Shortage is Not Temporary
“Manufacturers are expected to face economic uncertainty, the ongoing shortage of skilled labor, lingering and targeted supply chain disruptions, and new challenges spurred by the need for product innovation to meet company-set net-zero emissions goals.” ~ Deloitte
Manufacturing accounts for about 11 percent of U.S. GDP and employs approximately 8 percent of the U.S. workforce, but U.S. manufacturing jobs have declined from 19.6 million in 1979 to nearly 13 million by November 2022 – a significant 56 percent decrease when adjusted for population growth.
Yet, as of August 2023, 616,000 U.S. manufacturing job openings are still needing to be filled. The industry’s talent shortage, per Betterworks Engage, can be attributed to:
- Outdated perceptions that manufacturing jobs aren’t safe, clean, or progressive
- Misconceptions by younger generations that manufacturing lacks competitive wages
- Perceived lack of investment in employee growth and development
- Not enough STEM graduates with specific skill sets and abilities to meet demand
- A quarter of the industry’s skilled worker base retiring, with more to come in the next decade
In fact, 77% of manufacturers say this shortage is not temporary and there will be ongoing difficulties attracting and retaining workers in the industry.
The manufacturing skills gap in the U.S. could result in 2.1 million unfilled jobs by 2030, according to a study by Deloitte and The Manufacturing Institute. The cost of those missing jobs could potentially total $1 trillion in 2030 alone. This is true for both talent skilled in the design and operation of old and new machinery, as well as the usual positions that are always needed across manufacturing companies to conduct business.
To attract new talent from various sectors, manufacturers must bridge the gap between the expectations of job seekers and the reality of manufacturing jobs, as highlighted by a Deloitte Global Human Capital Trends study. It's crucial for these companies to focus on widening their talent pool, fostering inclusive work environments, and committing to ongoing skill development to ensure future success.
Key Findings from NEI’s Global Relocation’s 2023 All Benefits Survey
To address these shortages, manufacturing industry Talent Management and HR teams will have to evolve and maximize relocation efficiency and effectiveness to secure talent and retain employees. This starts with examining the benefits used today and ensuring they are ready for tomorrow.
Notable findings from Manufacturing companies participating in NEI Global Relocation’s 2023 U.S. Domestic All Benefits Survey include the following:
Partial Lump Sum
- Manufacturing companies tend to favor a Partial Lump Sum program to cover certain benefits such as temporary living, home finding, return trips, final move and miscellaneous expense allowance.
- A partial lump sum was offered by 31 – 67% of Manufacturing companies (depending on employee level) as compared to 30 – 51% of participants in all industries combined.
Economic Impact on Policy
- Unlike other industries, Manufacturing has not increased COLA, MIDA or Lease Cancellation due to economic changes, choosing instead to stay the course.
- Many companies in NEI’s U.S. Domestic All Benefits Survey (all industries combined) have reviewed and revised policy components to adjust to the changing market.
Home Sale Trends and Responses
A strong sellers’ market over the past few years has caused many companies in multiple sectors to tighten up their home sale programs, scaling down benefits to save money without significantly impacting employees. As the market pendulum starts to swing back to the buyers’ favor, companies are beginning to consider ways to enrich their home sale programs again.
- BVO is preferred over GBO by Manufacturing participants. BVO is offered by 7 – 47% of Manufacturing participants compared to 5 – 33% of participants in all combined industries.
- GBO is offered by 0 – 35% of Manufacturing participants compared to 1 – 43% of participants in all combined industries.
- Loss on Sale is offered by 0 – 20% of Manufacturing participants compared to 1 – 34% of participants in all combined industries.
Tax Treatment
- Manufacturing participants were less likely to gross-up origination services(e.g. partial lump sum, home sale reimbursements, miscellaneous expense allowance), and yet more likely to gross-up destination services (e.g. temp living, rental finding assistance, home finding trip).
- Of Manufacturing participants, 45% complete year-end true up calculations compared to 34% of participants in all combined industries.
In summary, manufacturing companies lean towards more conservative relocation policies, such as favoring Partial Lump Sum programs and maintaining steady course on COLA, MIDA, or Lease Cancellation policies despite economic shifts. This approach is distinct from broader industry trends, where companies are revising policies to adapt to market changes.
A company within the manufacturing sector that adopts a more robust and forward-thinking relocation policy not only differentiates itself but also has a golden opportunity to secure and retain the industry's best talent. As the landscape evolves, those willing to enhance their benefits in thoughtful ways could obtain a sizable competitive advantage.
Investing in Future Competitiveness Today: The Role of Relocation
“Manufacturing is no longer the old-fashioned assembly-line industry of yesteryear. Manufacturing today is taking center stage as an electrifying industry full of possibilities.” ~ Forbes
With expense reduction top of mind for many, it is imperative for Manufacturing companies to identify and consider cost savings opportunities, but also leverage innovative relocation services, technologies, and expertise when addressing talent needs.
NEI Global Relocation strives to be in complete alignment with each client’s priorities, business objectives, and talent management goals.
When choosing the best global relocation management partner, look for a trusted, stable firm with experienced professionals and extensive global networks. A partner that will deliver you the best return on investment, proactively advise you on current and future trends, and support your efforts to secure and relocate talented candidates.
For more information, please contact your NEI representative.
About NEI Global Relocation
NEI is a certified Women’s Business Enterprise headquartered in the U.S. with in-region offices and teams in Switzerland and Singapore. As a full service, global relocation and assignment management company that partners with clients across the globe to provide consultative guidance and solutions, NEI has over 200 clients including many Fortune 500 and Fortune 1000 corporations and we support client Tier 1 and Tier 2 supplier diversity goals each year. For more information and other articles, see www.neirelo.com.
The above article is provided for informational purposes only. Please consult your tax, legal, or accounting advisors before making any decisions or transactions.